For centuries the influence of Venice had stretched far and wide. But by the late 1600s Venetian influence in glass technology began to fade as a revolutionary recipe created in England in 1674 became popular. George Ravenscroft is credited with the creation of lead glass (then known as flint glass due to the use of powdered flint as silica) in which lead oxide was added to the molten glass batch. Lead glass was not only stronger and more durable but also clearer than Venetian glass. The large proportions of lead in the glass, up to 40% in some glasses, means it is very stable. The network of molecules in the glass is tightly held together so when the glass is struck the network cannot absorb the shock and instead vibrates in place. This gives lead glass a characteristic ring when tapped. This characteristic ring is absent in Venetian glasses.

Lead glass is less viscous and takes much longer to cool and solidify than the façon de Venise glass. This dictated the sort of styles possible in lead glass. The fanciful designs of Venice gave way to more practical and straightforward shapes. Individual glasses were now constructed from three components, the foot, the stem and the bowl, made separately and then joined together in a production line typical of the industrialisation taking place at the time. Ornament was added to the glasses by engraving patterns onto them or in the form of decorative stems. Air twist stems were briefly popular around 1750 but were replaced by opaque twist stems (also known as cotton twist). English glass blowers used the filigree technique invented in the 16th century to produce increasingly complex patterns in the stems of glasses. One column of threads was sometimes surrounded by another, creating beautifully intricate interweaving designs.
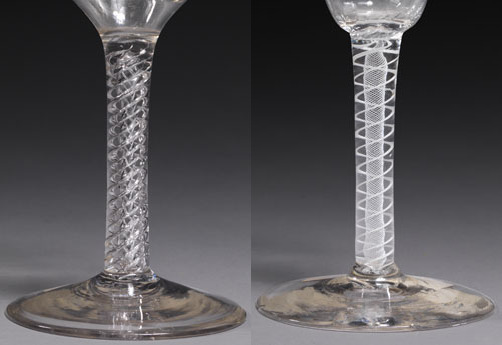
Back to Filigree Drinking Glasses