Habitation
by César
The sculpture Habitation was created from over 100 separate pieces of scrap metal. These items were collected from a junkyard on the outskirts of Paris and welded together by the French artist César in 1960.
Habitation will be displayed at The Science Museum in London in 2020, as part of the McQueens Illuminating Objects partnership while The Courtauld Gallery is temporarily closed for a major refurbishment programme. The connection to The Science Museum provides an opportunity to focus on the scientific ideas and techniques embodied in the sculpture. These were of abiding interest throughout César’s career. This webpage has been researched and written by Jack Monaghan, a postgraduate student in Science Communication at Imperial College London.
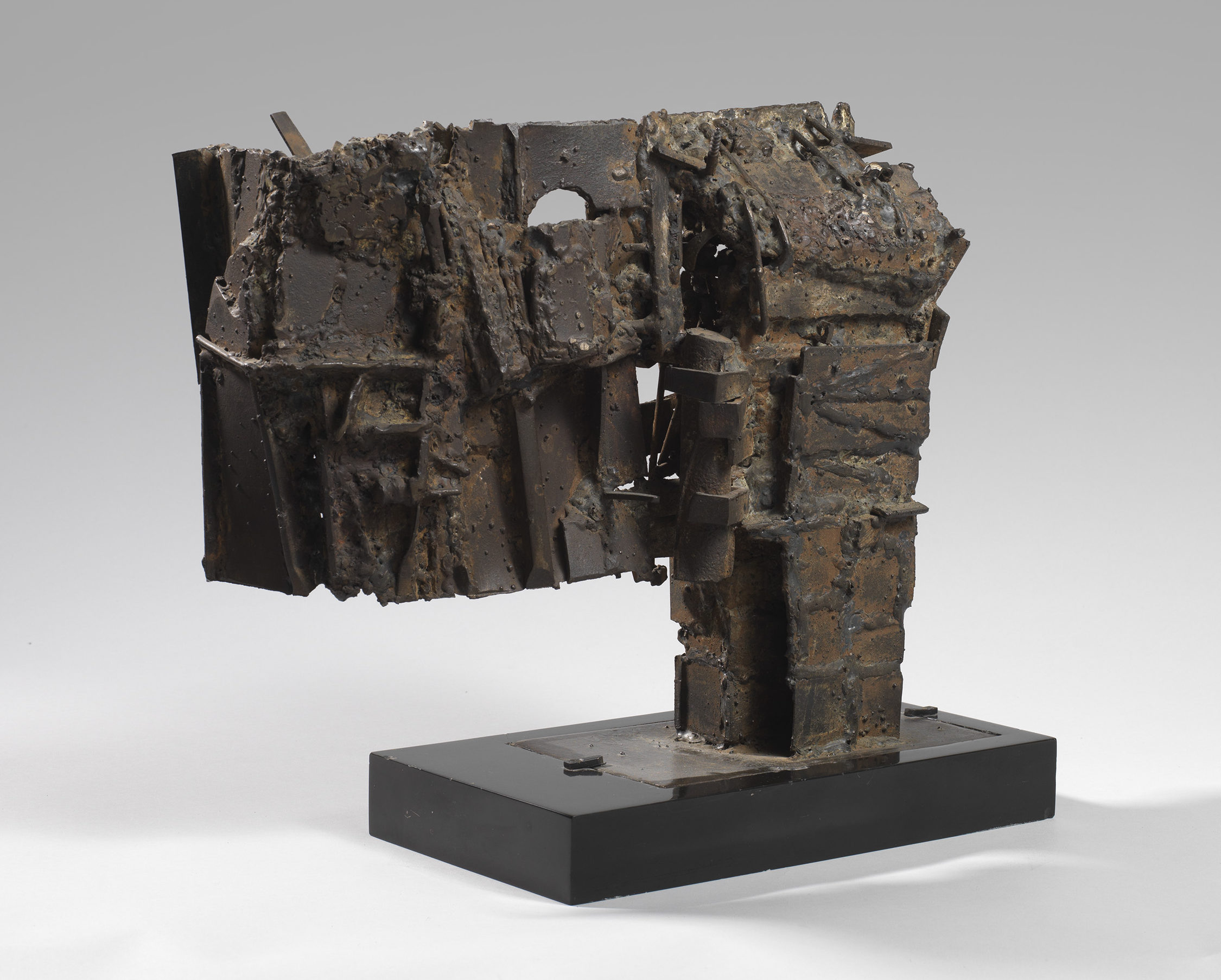
On this page you can find:
> César – the Steel Poet The life and work of the man behind the sculpture.
> Molten Raw Materials How dust from the explosion of a star was mined, smelted and chemically converted into the steel that makes Habitation.
> Electric Cement How thousands of bolts of man-made lightening from a welder’s electrode fused the sculpture together.
> From Junkyard to Gallery A closer look at the plethora of scrap objects Habitation is made from.
'I'm a peasant, a self-taught man, I didn't go to school, I played truant. Chance meetings in cafes mattered more to me than books. The street taught me the lessons of life.' César
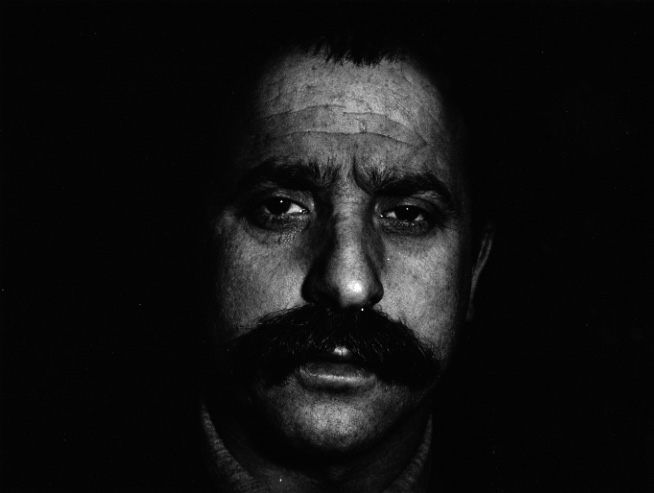
César – The Steel Poet
César Baldacinni (1921-1998) was born to Italian parents, in the bustling port city of Marseilles in Southern France. He spent his childhood in Belle-de-Mai, a working-class quarter of the city, where his father ran a small wine business, and his mother worked as a cleaner.
Though he left school at 12 to work for his father, César had an interest in drawing from an early age. He developed his artistic skills at preparatory classes at the city’s art school – the Ecole des Beaux-Arts of Marseilles. At age 17 he gained a scholarship to become a fully enrolled student and studied at the school for five more years.
In 1943 César was accepted into the most prestigious art school in France – the Ecole Nationale Supérieure des Beaux-Arts, in Paris. He, again, began at the school as a temporary student to allow him to travel back frequently to his family in Marseilles, only becoming a permanent student in 1946.
It is while studying in Paris that César was exposed to modernist art through the work of Swiss sculptor Alberto Giacometti. Giacometti’s studio was close to César’s lodgings, and the pair lived together for a time. César extended his time at the Ecole des Beaux-Arts until 1954 – longer than was normal. This allowed him access to materials and studio space that it would otherwise have been difficult for him to afford.
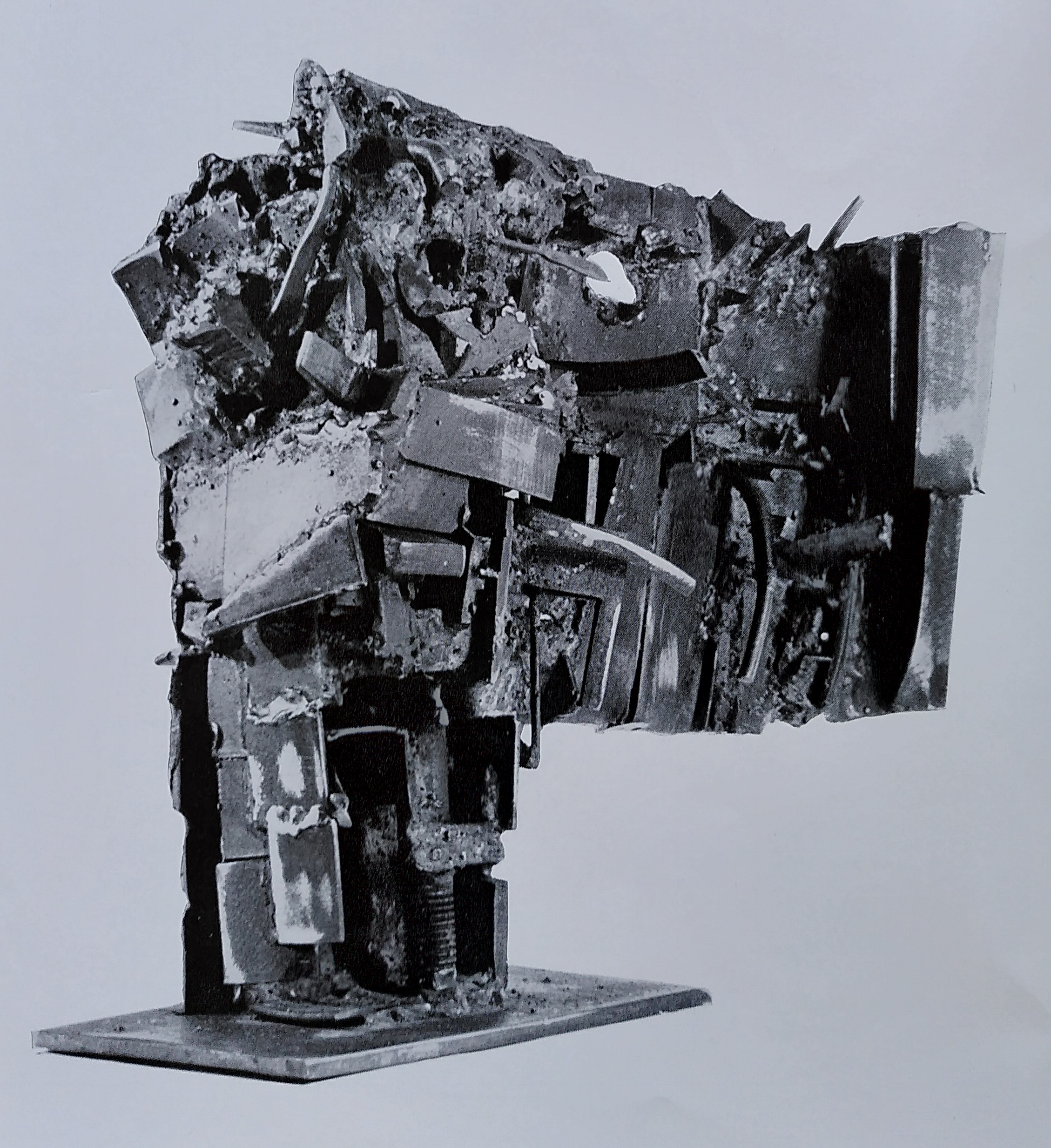
After leaving art school César set up his own studio inside a metal furniture factory called the Matérial Malma. He had been introduced to arc-welding six years before, and in the factory he had the tools to weld independently. It was also around this time that César started using scrap metal in his work. He visited the Société Française des Ferrailles, a large scrap metal yard that was to be the source for much of his material. Both the yard and studio were in Saint-Denis, a sprawling suburb to the North of Paris. It was with pieces of scrap from this yard, welded together in his furniture factory studio, that César would make the piece titled Habitation.
César’s first solo exhibition was in 1954 at the Galerie Lucien Durand in Paris. His first exhibition in the UK followed three years later, at the Hanover Gallery, London. And three years after that, at the same London gallery, Habitation was first displayed.
Habitation and a year of change
Much was changing in César’s personal life in the years leading up to the creation of Habitation. In 1958 his first and only child was born – his daughter Anna. At the time of her birth César was not married to Anna’s mother but to another woman, Maria Astruc. He and Maria divorced in 1959, and the following year César married Anna’s mother – Rosine Groult. The title of this sculpture – Habitation, meaning a home or dwelling – may have had particular resonance following two years of upheaval in his private life.
‘I have had many lives, many houses, many periods. I do not negate any of it. I only ask that there be several readings whereby one finds the academic, the need to renew, the quotidian, the bearing witness to industrial civilisation, abstraction, the fascination with new materials, my desire to restore order, my urge to destroy, to rebuild.’ César

1960 was a year of professional change too. It was in this year that César joined a group of artists who called their work Le Nouveau Réalisme’ . These Nouveaux Réalistes, or New Realists, emerged from the French avant-garde, and presented ‘a poetic recycling of urban, industrial and advertising reality’. The group, led by the art critic Pierre Restany, called their vision of reality ‘Modern Nature’.
It was also in this year that César first created the works that would catapult him from a well respected artist to an international celebrity. These were his compressions.
César’s compressions were artworks made from cars and other metal objects that had been crushed in a hydraulic press. César began creating them in 1960 after seeing a hydraulic press in action – first on television, and later when one was installed, much to his excitement, at his local scrap yard in Saint-Denis. In 1960 César presented three of these compressed cars in a piece entitled Trois tonnes at the Salon de Mai (an exhibition of new work held in Paris each year).
Habitation was exhibited in a solo show at the Hanover Gallery, London, in November, 1960. The work was displayed alongside 29 other pieces, both in César’s earlier style of welded steel sculptures (called fers), and some of the first of his compressions. It was Restany, leader of the Nouveaux Réalistes, who wrote the introduction to César’s catalogue for the exhibition.
That Habitation was displayed alongside both César’s older and newer style sculptures is relevant. The sculpture exists at a moment when different paths stretched out ahead for him.
Habitation, a welded steel sculpture, embodies César’s art school training. There are even subtle resonances with Classical sculpture. Though the construction may be different, the techniques more industrial, it is still recognisable in form as a sculpture.
And yet, in comparison with many of the welded fers sculptures, Habitation is more abstract. Other sculptures have much clearer human subjects, such as L’Homme de Saint-Denis (1958). The compressions, on the other hand, are even further from conventional sculpture. Most strikingly César did not make these sculptures, but rather he ‘directed’ them. He would select a car or other metal object, place it into the hydraulic press, then turn on the power and the machine did the rest.
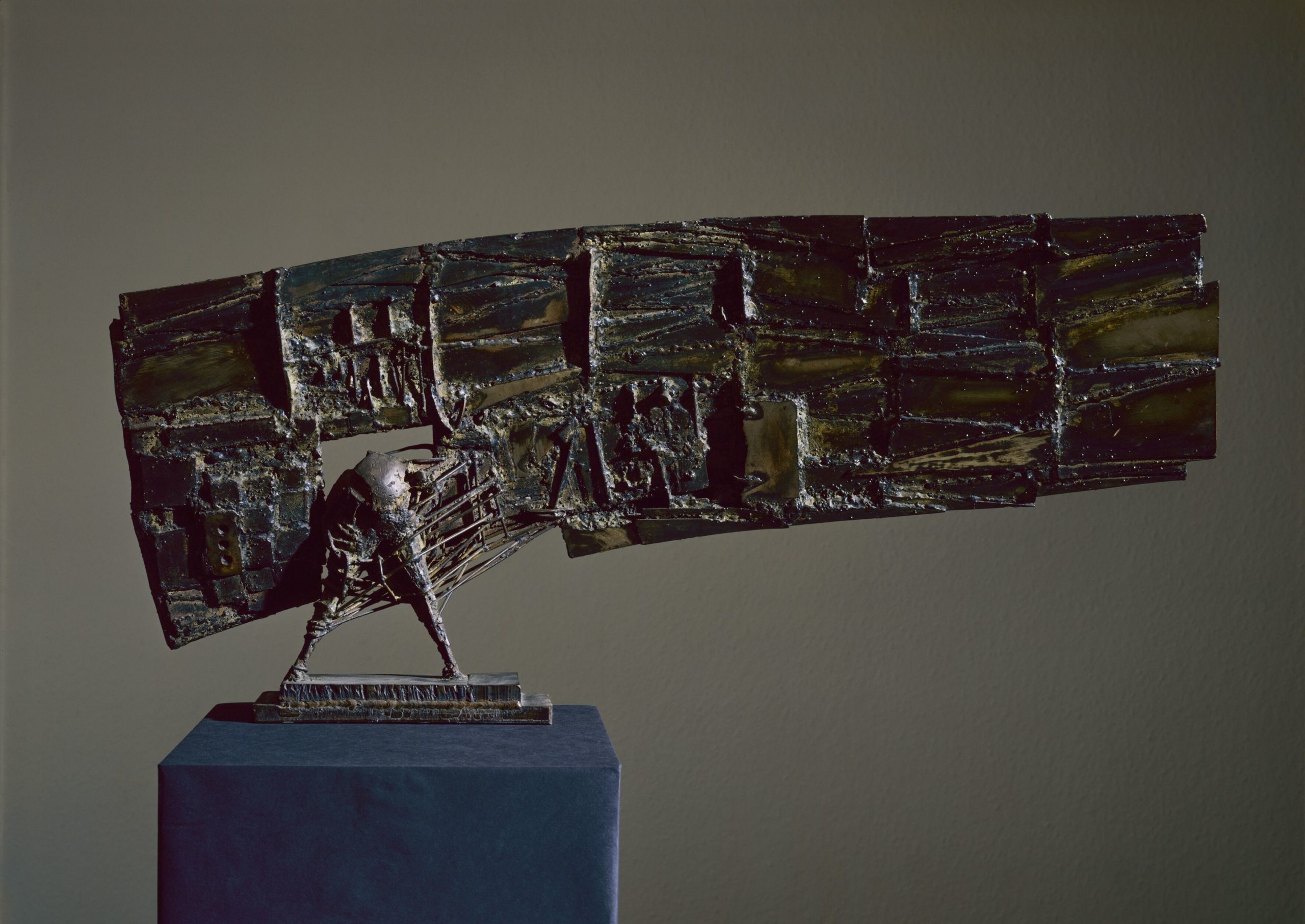
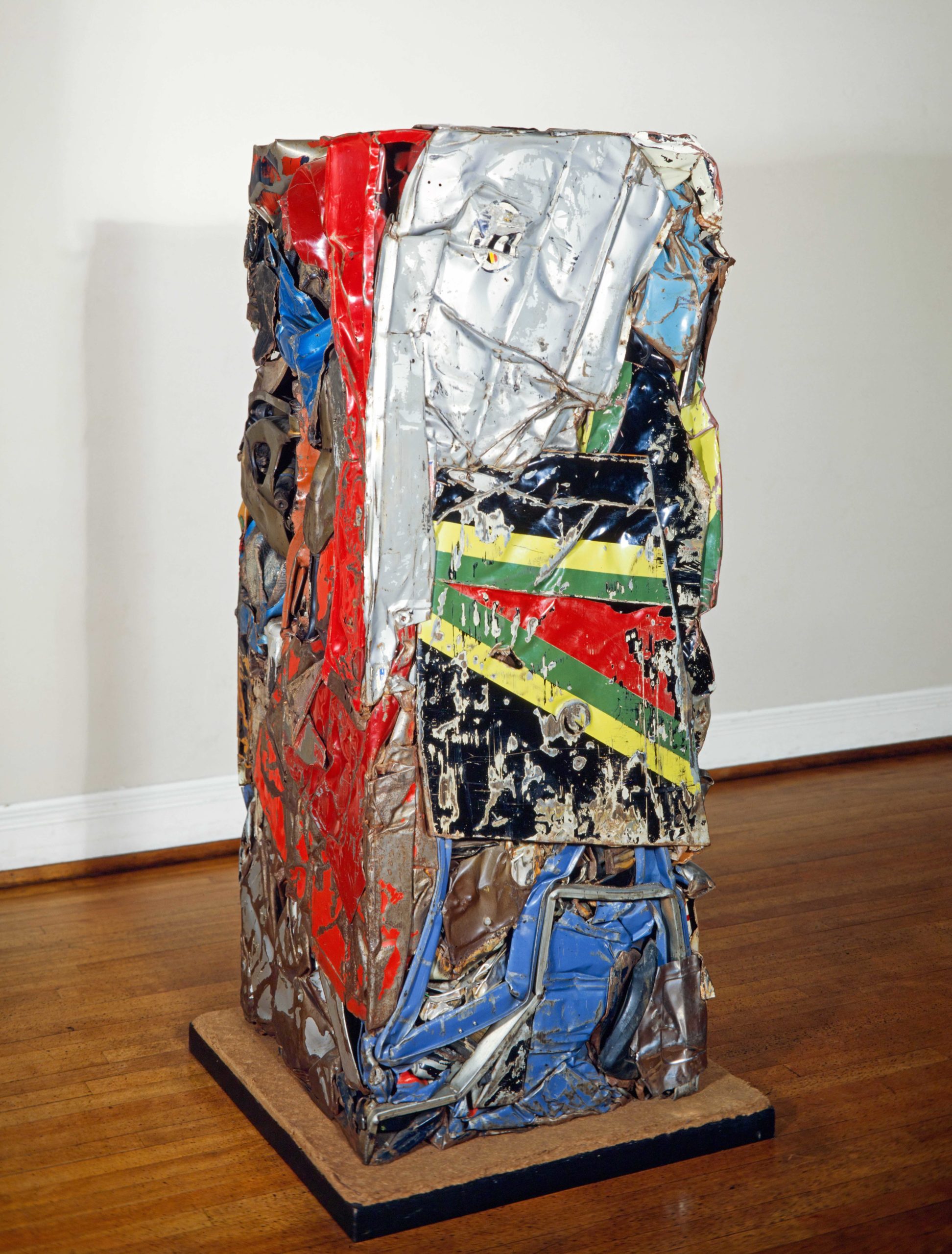
Habitation comes to the Courtauld
Habitation was sold by the Hanover Gallery to Dr. Alistair Hunter in 1961. Dr. Hunter was a keen collector of contemporary art and, at the time of the purchase, was an executive member of the Tate Gallery’s Contemporary Art Society. He would later become Honorary Keeper of Contemporary Art at the Fitzwilliam Museum in Cambridge. After his death in 1983, Habitation was bequeathed to The Courtauld Gallery, arriving in the collection in 1984 along with more than 20 modern British paintings. A fellow member of the Contemporary Art Society described Hunter as ‘one of the most intelligent and imaginative collectors of the post-war era’.
After Habitation
After 1960 César continued to make both fers and compressions. He also experimented with other forms that played on science and technology. These included: his empreintes (imprints) of enlarged human body parts, the most well known examples of these is his Pouce (Thumb) sculptures; and his expansions in which he used expanding plastic polymers to make unpredictable shapes.
César also cultivated a flamboyant celebrity status, with tailored suits and dramatic public demonstrations. At times this meant that his work was not taken seriously by the art world. The architect Jean Nouvel, a friend of César’s, described that ‘César did not project the image of an intellectual artist. And because he liked to live and laugh and could be seen at smart Paris parties, some people thought he was frivolous… but the real man was hidden behind that.’
In 1975 César gave his name to the annual French film awards (the equivalent of the Oscars). He is one of France’s most celebrated 20th century artists, receiving both the Legion of Honour and the National Order of Merit. César continued to make art until his death, aged 77, on 8th December 1998.
‘The artist’s life was itself the primary artwork, and the tangible evidence of artistry merely a by-product’ The Times Obituary to César, 8th Dec 1998
The great opportunity of contemporary sculpture lies in its adventure with iron. Art Critic and César's friend Pierre Restany
Molten Raw Materials
Habitation is constructed from ‘ferrous material’, meaning iron-rich metal alloys, and most of the items that make up its structure are steel. Steel is an iron alloy – meaning it is a mixture of elemental iron and another element, carbon. The amounts of these two elements vary depending on the type of steel, with iron the more abundant by far.
Habitation contains scrap objects made up of a range of different steel types – from the Low Carbon or Mild Steel used to make the steel wire (carbon content between 0.05-0.25%) through to the Ultra High Carbon Steel used to make the metalwork punches (carbon content of up to 2%). The amount of carbon changes the material properties of the steel objects, and also how easy or difficult it would have been for César to weld them.
This section examines the full timeline of the metal which makes up Habitation. It begins with the formation of iron atoms at the beginning of our solar system, through to the extraction from the earth as iron ore, the processing of iron ore into steel, and what happens to this steel at a scrap metal yard like the one César visited.
Origins of Elemental Iron
The Habitation sculpture contains 12.5kg of steel. This means it houses over one hundred million billion billion atoms of iron (that’s 100,000,000,000,000,000,000,000,000 atoms). Each of these atoms was created by nuclear fusion in the supernova of a star that exploded long before the Earth existed. Nuclear fusion takes atoms and forces their nuclei together under huge pressures and temperatures to make new, larger atoms. This stellar explosion is the beginning of the timeline for the materials of Habitation.
Human Extraction of Iron
Iron is common on Earth, comprising around 5% of the Earth’s crust by weight. However iron likes to react with other chemical elements to form compounds, as is evidenced by the colour of Habitation. The dull oranges on the surface of Habitation are areas where the iron atoms have reacted with oxygen in the air to form iron oxide, commonly known as rust.
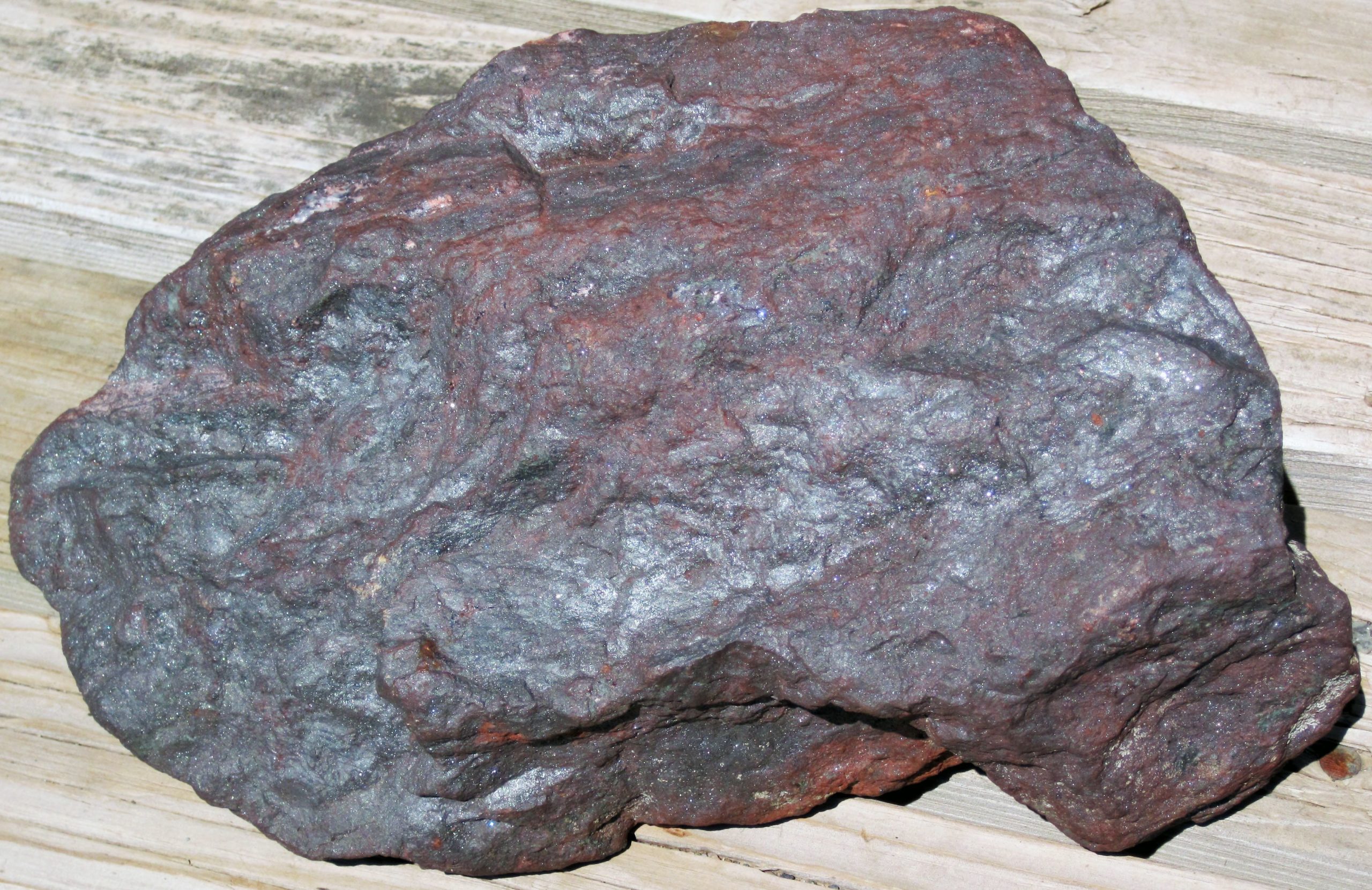
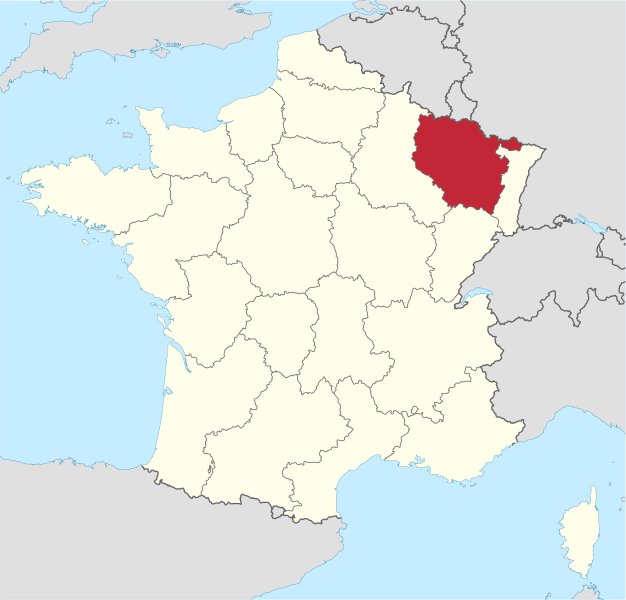
The most likely source for the iron in Habitation is the Lorraine region of North Eastern France (highlighted red on the map). During the 20th century this area was mined extensively, producing around 95% of France’s iron ore.
Lorraine ore is called Minette and the sedimentary rock it comes from was laid down during the Mid to Late Jurassic (165-200 million years ago). The rock has low iron content compared with other ores, and is high in phosphorus.
The name Minette can be translated from French to mean ‘little mine’ or ‘little vein’. However, the Lorraine deposit is one of the largest iron ore deposits in the world. The peak of iron ore production in Lorraine was during 1960, the same year as the construction of Habitation. From then on production declined, and the last mine in the region closed in 1997 with approximately 3 billion tonnes of ore still in the ground.
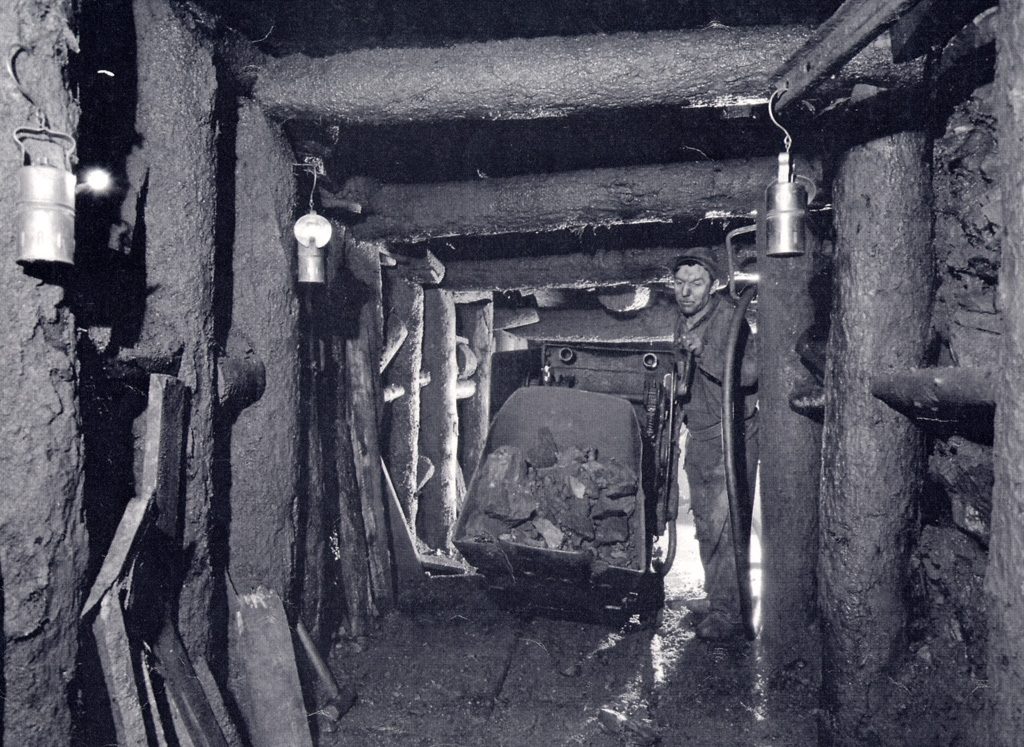
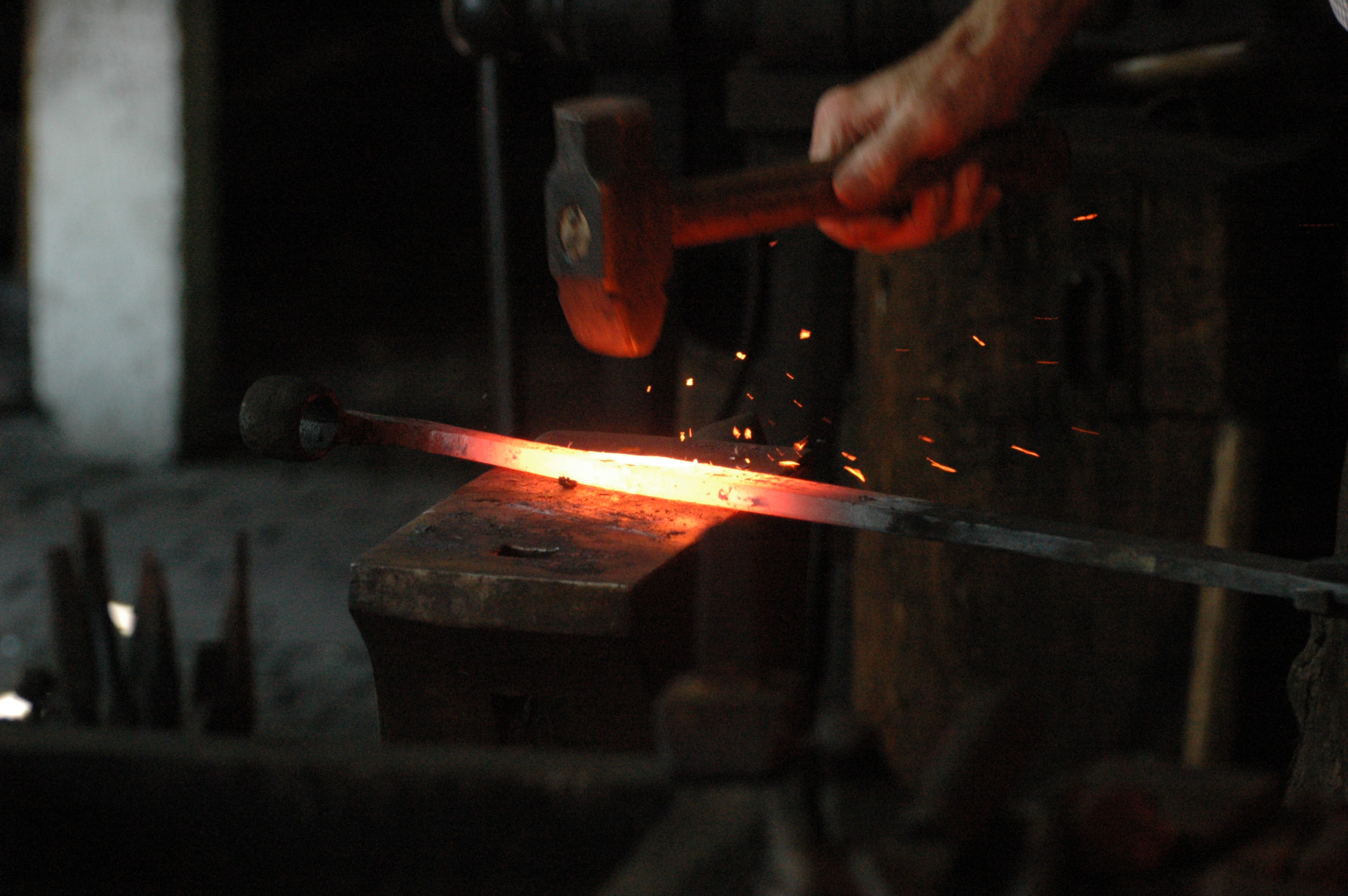
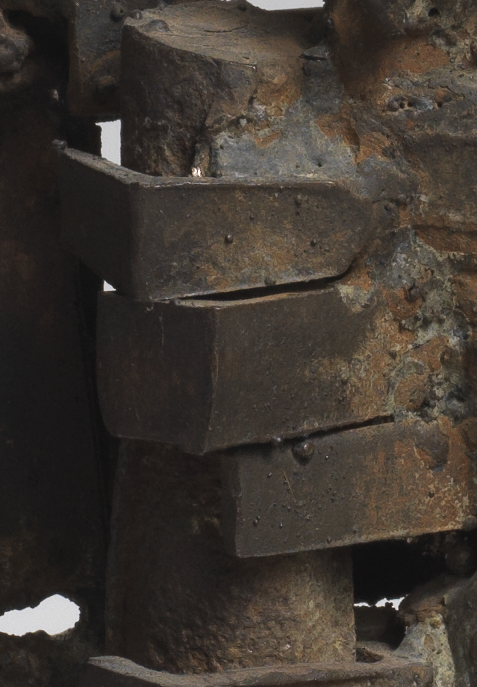
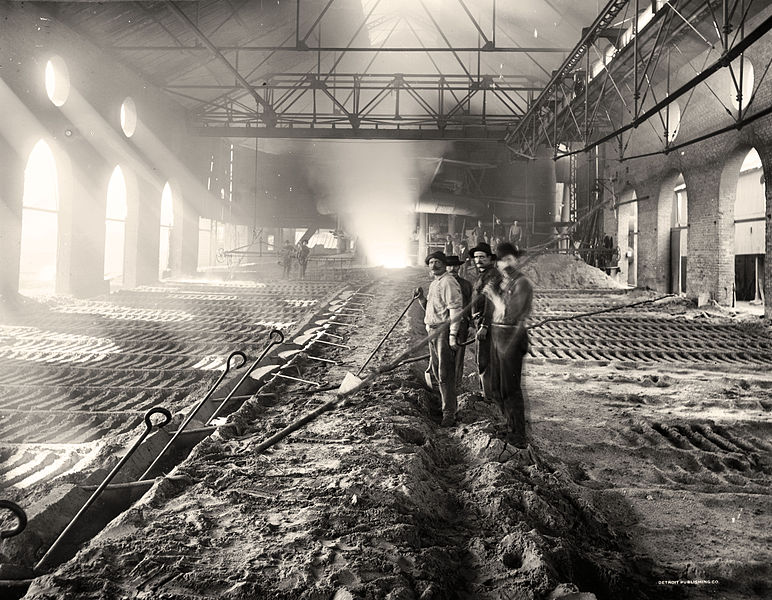
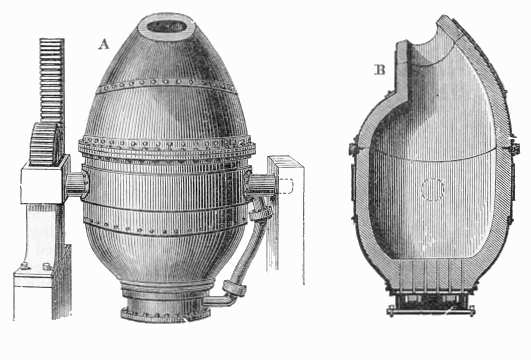
Three types of Iron
Once extracted from the ground, iron can be processed into three broad types of iron alloy: wrought iron, cast iron, and steel.
Wrought iron was the most common iron alloy for centuries. Pure iron has a very high melting temperature (15360C) and this temperature could not be obtained in early furnaces. Wrought iron was formed instead by mixing the ore with charcoal and heating to around 11000C. This process, known in chemistry as reduction, allowed the iron in the ore to melt at a lower temperature and escape from the ore as a solid ‘bloom’ of almost pure iron. This bloom was then hammered to remove impurities. This was known as forging or working the metal, thus the name wrought (meaning ‘worked’) iron.
By the mid 20th century, wrought iron had become much more expensive than other types of iron alloy. For this reason it was used sparingly and would have been rare in the Paris scrapyard César visited. There appears almost none of it in Habitation. However, there may be one small piece of wrought iron visible on the sculpture. The iron bar (shown here) is around 15mm across and sits half way up one side of the sculpture’s central trunk. The surface of the bar has a rougher, pitted weathering pattern that is visibly different from the smoother steel sheets that surround and partially obscure it. This may indicate that the bar is wrought iron. However, it could alternatively suggest a steel bar that has weathered differently due to increased exposure because it had been in the scrap yard for longer than the other scrap objects César selected.
As furnaces improved over time, another type of iron could be produced – Cast iron. First the ore was heated to around 12000C in a blast furnace. Although pure iron cannot melt at this temperature, iron containing carbon and other impurities can, and this impure carbon runs off the ore and is collected in small pools which cool to form ingots.
The iron ingots that resulted from melting iron ore at this higher temperature were known as pig iron. This was because the branching moulds traditionally used to cool the metal resembled piglets suckling from a sow. Though more brittle than wrought iron or steel, this pig iron has the advantage that it can be remelted and poured into moulds to make complex shapes. For this reason it is mostly used for decorative or specialised purposes. It is unlikely that there is any cast iron in César’s sculpture.
The final category of iron alloys is steel. Steel has a lower carbon content than cast iron. Though the process of steel production has changed significantly over time, the technique which made Habitation possible was invented in 1856 by the British engineer Henry Bessemer and adapted for the phosphorous-rich ore found in France by the two cousins Percy Gilchrist and Sidney Gilchrist-Thomas.
This process, known as the basic Bessemer process, involved pouring molten iron from a blast furnace into a converter. In the converter air is blown through the iron, and this air reacts with the carbon, silicon, and manganese impurities commonly found in cast iron to form oxides which can be removed from the top of the liquid iron as what is known as slag. The Bessemer process was incredibly quick and allowed steel to be mass-produced for the first time.
By the 1950s newer steel production processes were replacing the Bessemer converters, and so it is likely that the steel in Habitation was created using a different method.
Steel is by far the most common metal alloy used today, comprising 95% of all metal used globally. In 1960, the year César made Habitation, it is estimated that the global production of steel was 380 million tonnes per year. According to the World Steel Association, this figure has been rising steadily, and had reached 1800 million tonnes by 2018. Like Great Britain, France used to be one of the leading nations in the World in the production of steel. When César made Habitation France was the sixth largest producer in the world. Now it is fifteenth.
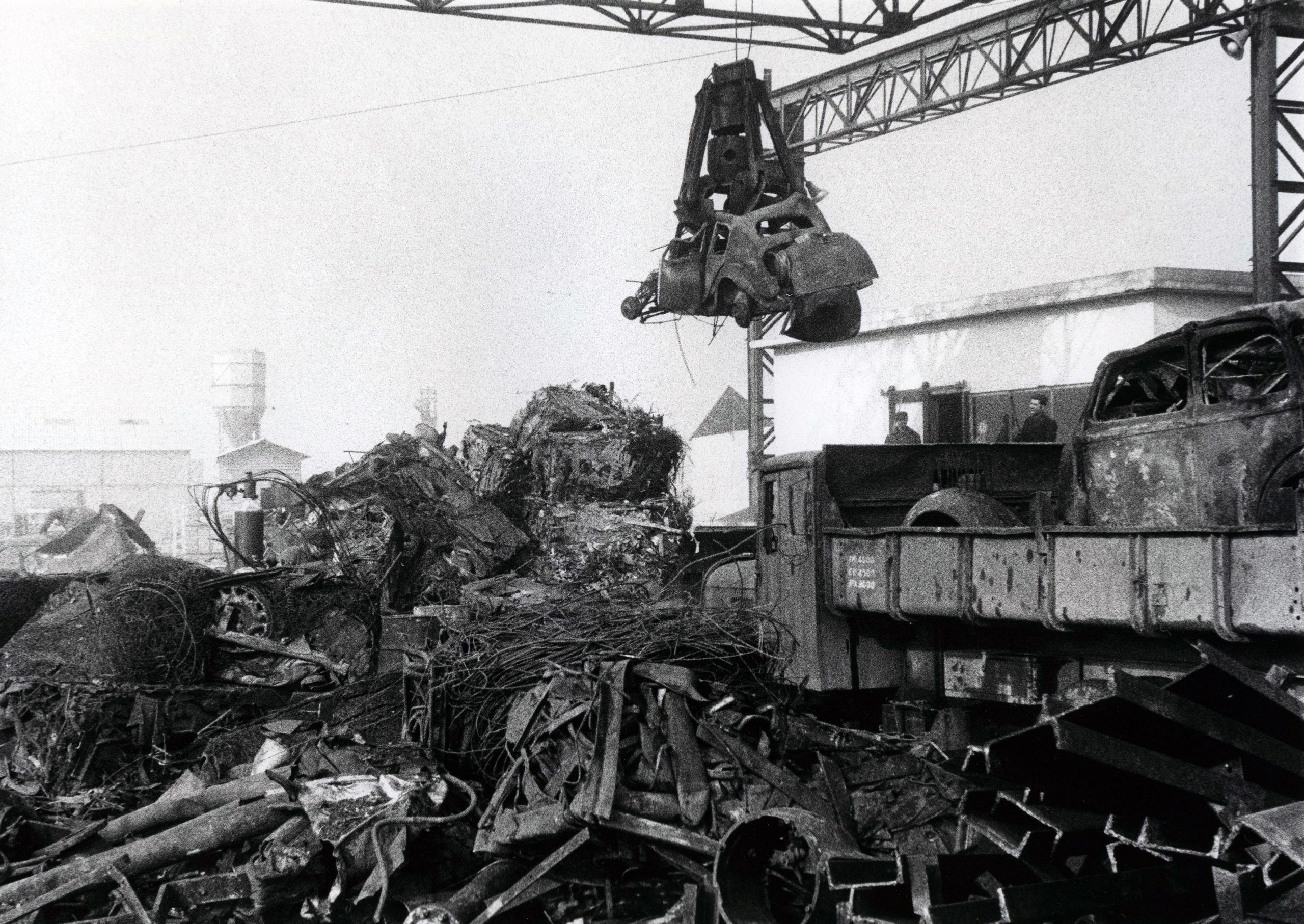

Scrapyard Steel
Processing iron ore into useable metal is expensive. For this reason iron/steel is now the most widely recycled material in the world.
Scrap yards are not simply rubbish dumps – they are places where metal is sorted into different types, before being sold to processing plants to be melted down and reused.
The scrap metal yard where César found the materials for Habitation was called ‘la Société Française des Ferailles’ (the French Scrap Iron Company) and was located in the sprawling suburb of Saint-Denis to the North of Paris. The scrap yard was a short distance along the Seine from his studio – inside a metal furniture factory in the town of Villetaneuse. The area of Saint-Denis was home to many large car and vehicle factories, and some of the scrap from these factories found its way to the yard and from there to César’s studio, where he made Habitation.
Steel for Peace
The importance of iron and steel for industry, construction and military applications has made iron ore sites places of vicious territorial fighting. This was true for France’s Lorraine region where some of the bloodiest battles of the first and second world wars were fought.
The French steel industry was vitally important politically in the decade leading up to César’s sculpture. In 1950, only five years after the end of the Second World War, French foreign minister Robert Schuman suggested that a centralised community for European steel production would be a way to make further war between Germany and France ‘not only unthinkable but materially impossible’.
What followed was the formation of the European Coal and Steel Community – an organisation of six European nations and the first international union which delegated power across multiple member states. This community laid the groundwork for what would become the European Union.
‘The pooling of coal and steel production should immediately provide for the setting up of common foundations for economic development as a first step in the federation of Europe, and will change the destinies of those regions which have long been devoted to the manufacture of munitions of war, of which they have been the most constant victims.’ The Schuman Declaration, 9th May 1950
This was the background in which César made his sculpture, and the raw materials from which he made it. But once he had the raw materials how did he fuse them together? This is the subject of the next section.
'A ton of melted iron is not like a blank canvas. You have to feel and master the material, make it yours. It has its own life.' César
Electric Cement
Once César had collected the pieces of scrap metal and returned them to his studio in Villetaneuse, he could begin building his sculpture.
His sculptural process was very different from those of a sculptor working in marble or bronze. Broadly speaking a marble sculpture starts as a large block of stone from which the sculptor removes material, so reducing its size to reach the desired form. Bronze casting requires the creation of a mould or moulds into which molten bronze is then poured and cooled to make the desired shape before the complex finishing processes can begin. The bronze, then, is redistributed – not changing in volume (like the Marble block), but in shape.
César’s method, in contrast, was not one of removal or redistribution but of gradual accumulation. The base material – the scrap objects, do not change size or shape, but rather are arranged in relation to each other. Starting from the base – a piece of scrap is welded on, welding another onto that one, then another onto that, and so on – gradually building up to the whole.
The method César used for joining his pieces of scrap together is known as manual metal arc welding (MMAW).
MMAW Method:
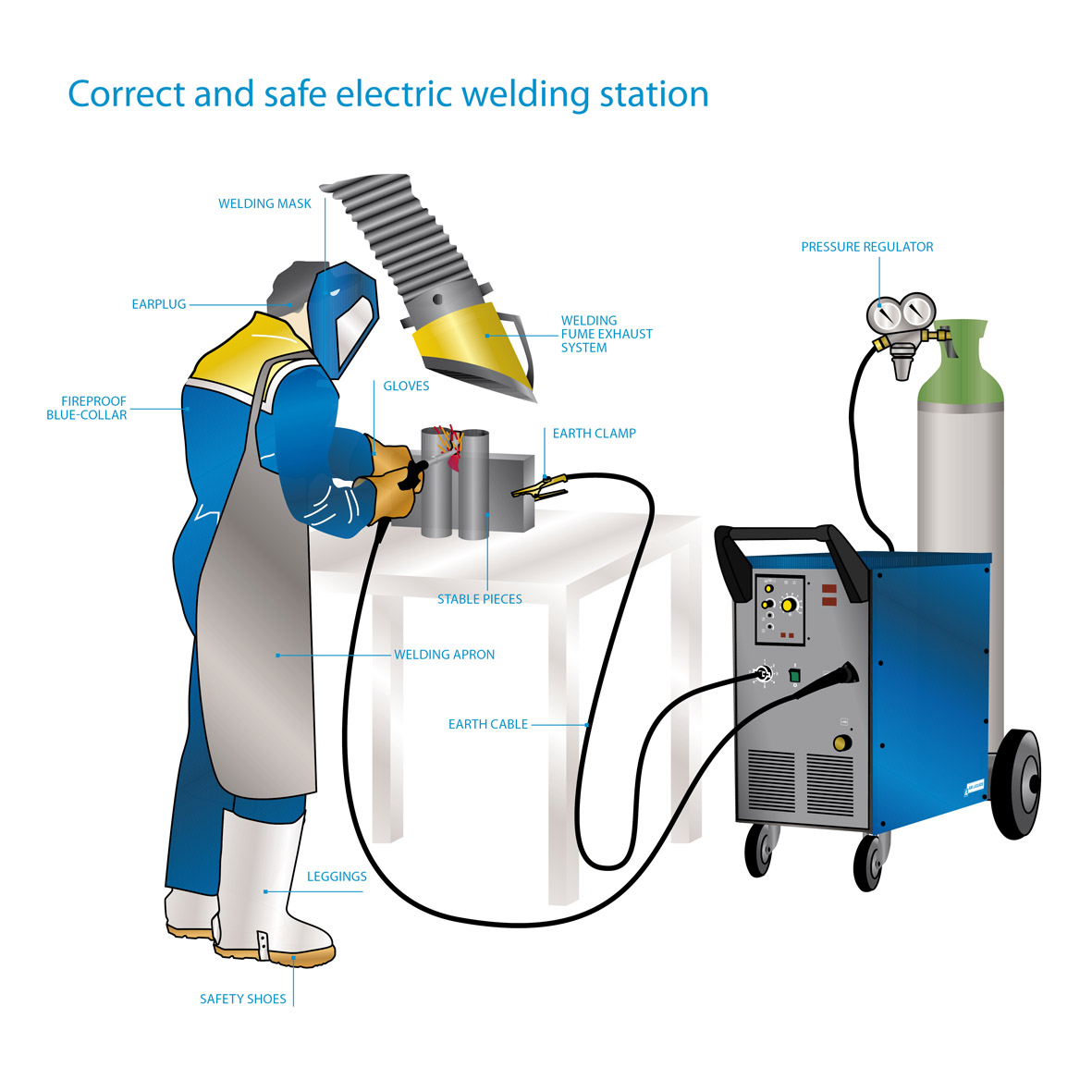
The core material of the electrode is usually similar or identical to the material being welded, and this core is covered in a substance known as flux. As César was largely welding steel it is probable that the electrode was also steel of a similar composition. Flux compositions change too, and it appears most likely that the electrodes used by César had a cellulose flux, however this is difficult to ascertain for certain.
2. The objects to be welded are called the base metal, and these are positioned on a metal work bench that is connected back to the power source by a ground clamp.
3. To begin welding the welder must ‘strike an arc’. This process requires the electrode to be lightly touched to the base metal then pulled back slightly. This demands some skill on the part of the welder – move the electrode too far or too quickly and the arc will break, move it too slowly and the electrode will fuse to the metal object.
4. Once the arc is struck the welder must maintain a distance of about 3mm between electrode and base metal. Across this distance, the electric current jumps – creating a metal arc similar to the effect of lightening. The electric current passes:
a. from the generator to the electrode,
b. from the end of the electrode, as an arc through the air, into the metal object,
c. through the metal object to the work bench,
d. through the ground clamp back to the power source.
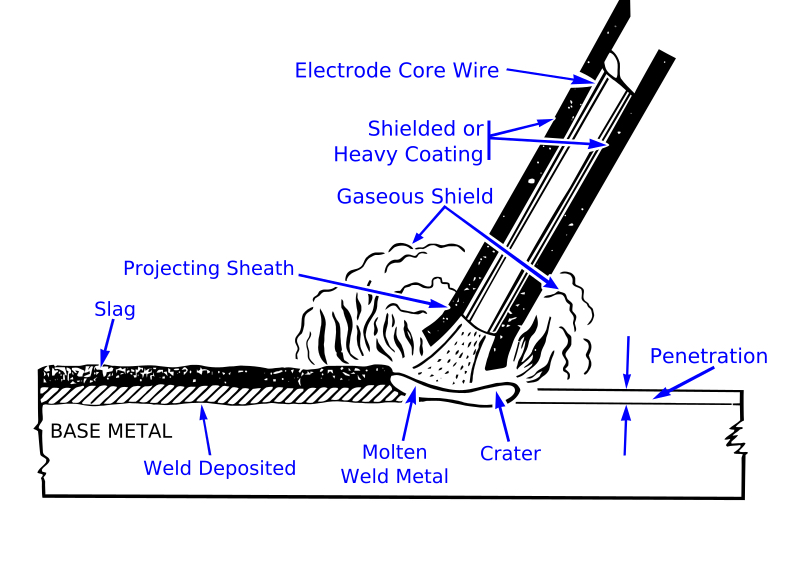
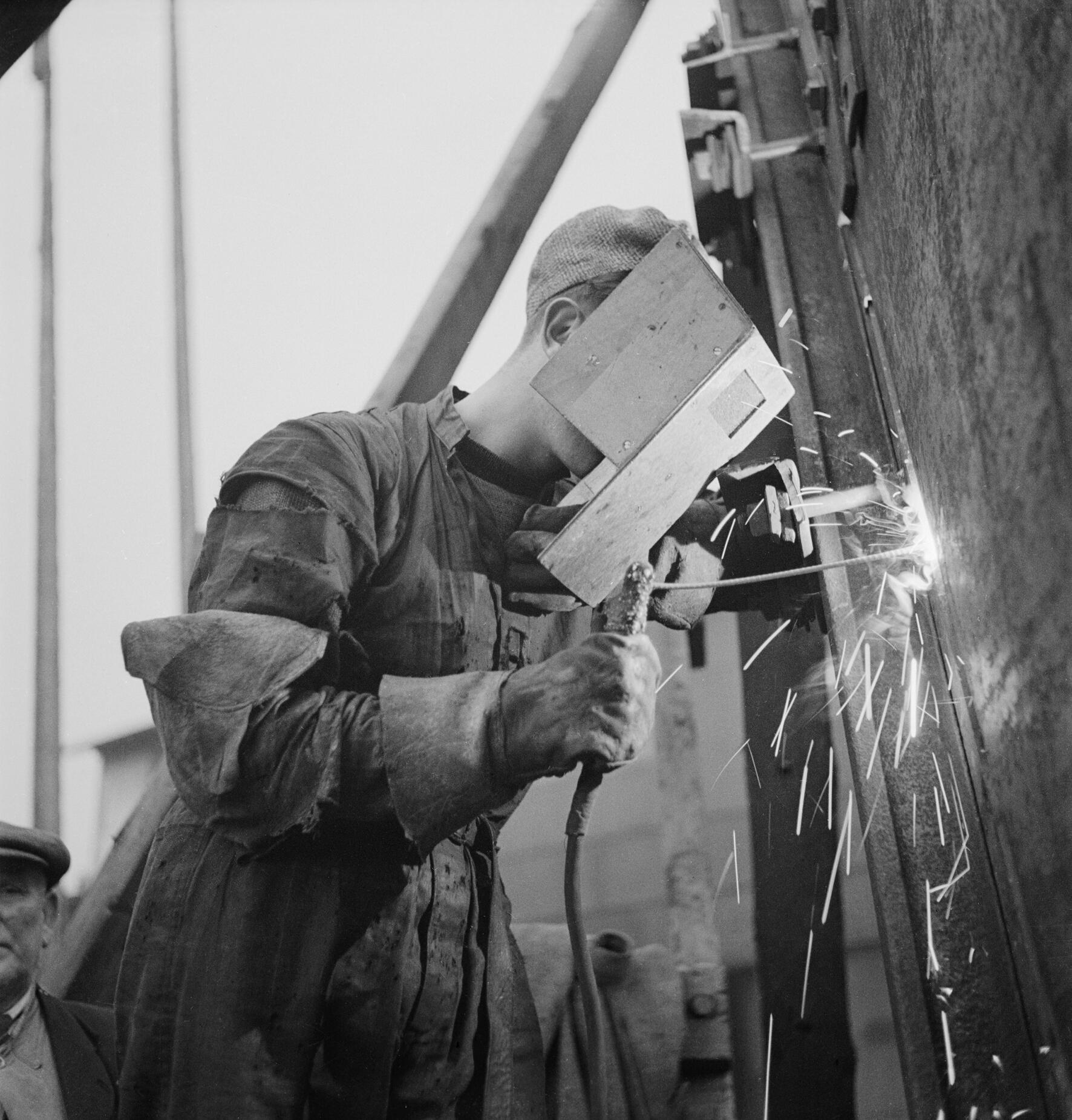
6. The flux on the outside of the electrode is also subject to the high temperature and disintegrates releasing both gaseous vapour and molten ‘slag’. Both the shielding gas and slag protect the molten weld pool from the surrounding atmosphere. Without these shielding materials the molten metal would react with gases in the air, weakening the resultant bond.
7. As the welder moves the electrode across the metal, away from the original point of arc-contact, the weld bead left behind cools, returning to solid metal and forming a very strong joint.
8. The electrode is consumed by the arc welding process, meaning that welding can only continue for a limited time before a new electrode will be required.
Because of the dangers of working with a large electric current in an exposed electric arc, welders wear thick rubber-soled boots to insulate them from the ground, they also wear a flameproof jacket or apron and gloves, as well as a mask to protect them from the bits of molten metal that fly off the electrode and create the characteristic blue welding sparks. The eye space on the mask is darkened to allow the welder to see what they are doing through the bright light created by the welding arc.
The process of welding – joining metals by heating them – had been known for millennia. The first instances of this was a process called fire welding – whereby sheets of wrought iron were heated and joined by hammering while white hot.
Arc welding, however, was only developed in the late 19th century after the technologies required to generate and harness electricity were developed.
The electric arc was discovered by the British scientist Humphry Davy in 1800, but it wasn’t until the 1880s that French and Russian engineers developed the idea of welding with an electrode arc torch.
Through the late 19th and early 20th centuries the technology was improved. With the expansion of industry and warfare in this period, as well as the increase in the ownership of personal metal items, the demand for welded metal increased.
Uses of MMAW
Because of its ease, versatility, and relatively simple machinery requirements, MMAW was one of the earliest welding techniques developed. It remains popular today. It is primarily used in repair work, industrial fabrication, and large steel construction.
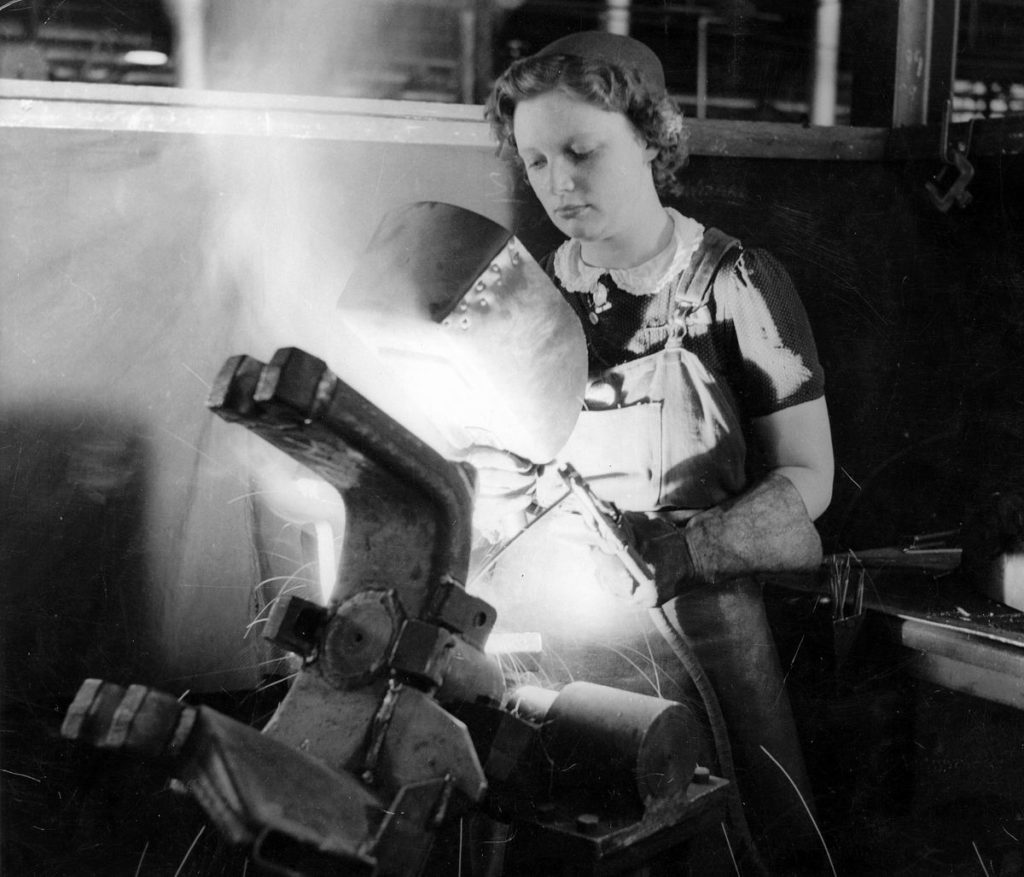
On the surface of Habitation we can see evidence of how César used welding on the sculpture.
Spatter
There are frequent examples of weld spatter on the work. Spatter refers to small solidified droplets of molten metal that were spat out of the weld area and landed on other sections of the base metal, appearing as small irregular balls on the surface.
Spatter is a common problem for welders looking to produce a neat finish. It can be caused by using too high a current, moving the arc too quickly, or stretching the arc too long. However, spatter can be cleaned off with relative ease. That spatter is visible on the final sculpture signals an intentional decision on the part of the artist, rendering what would be smooth, flat steel sheets more chaotic, irregular, disturbed.
The heat created by the welding arc melts the flux coating of the electrode. This molten flux mixes with the molten metal in the weld pool and floats to the top as a layer of impurity known as slag. This slag occurs in all MMAW beads, and welders wishing to create neat work spend much of their time cleaning it off the surface of their weld with a stiff wire brush.
César has removed slag in some areas of Habitation, but has chosen not to remove it in others. It can be seen on the surface of the steel as dull, darker patches with something of the appearance of lead (though this is not their composition).
In this image we can also see remnants of the artist’s mark. The wave-like striations moving along the weld from top right to mid left indicate the movements of César’s hand, holding the electrode and passing it slowly over the metal’s surface in short oscillating strokes.
On other areas of the sculpture we see a secondary effect called porosity. The small hollow rings raised on the metal’s surface indicate frozen bubbles that have popped on the base metal when it was still molten. When the weld pool does not receive enough protection from the atmosphere by the shielding gas, the molten metal can absorb nitrogen, oxygen, and hydrogen from the air. Some hydrogen and oxygen can also enter the weld pool from the flux itself in the form of absorbed water.
As the metal subsequently cools these nitrogen, oxygen and hydrogen gases are expelled in bubbles that pop on the surface. Were this an industrial weld job these bubbles could be very dangerous as they would seriously undermine the structural integrity of the joints. In the artwork they give the metal a living, breathing quality – not of a still and inert solid substance, but of something bubbling, seething, energetic and alive.
Finally there are areas of the sculpture where the amount of weld is much greater than is necessary for a solid join. Here the weld bead or pool area is more than a centimetre across, and often with a texture that is jumbled and bumpy, in stark contrast to the flatness of the sheet steel.
It is possible that César created these on the sculpture by repeated application of the electrode. However, it is more likely that he used a gas-flame to melt the metal in situ, rather than an arc.
Examination of the Junk Objects in Habitation
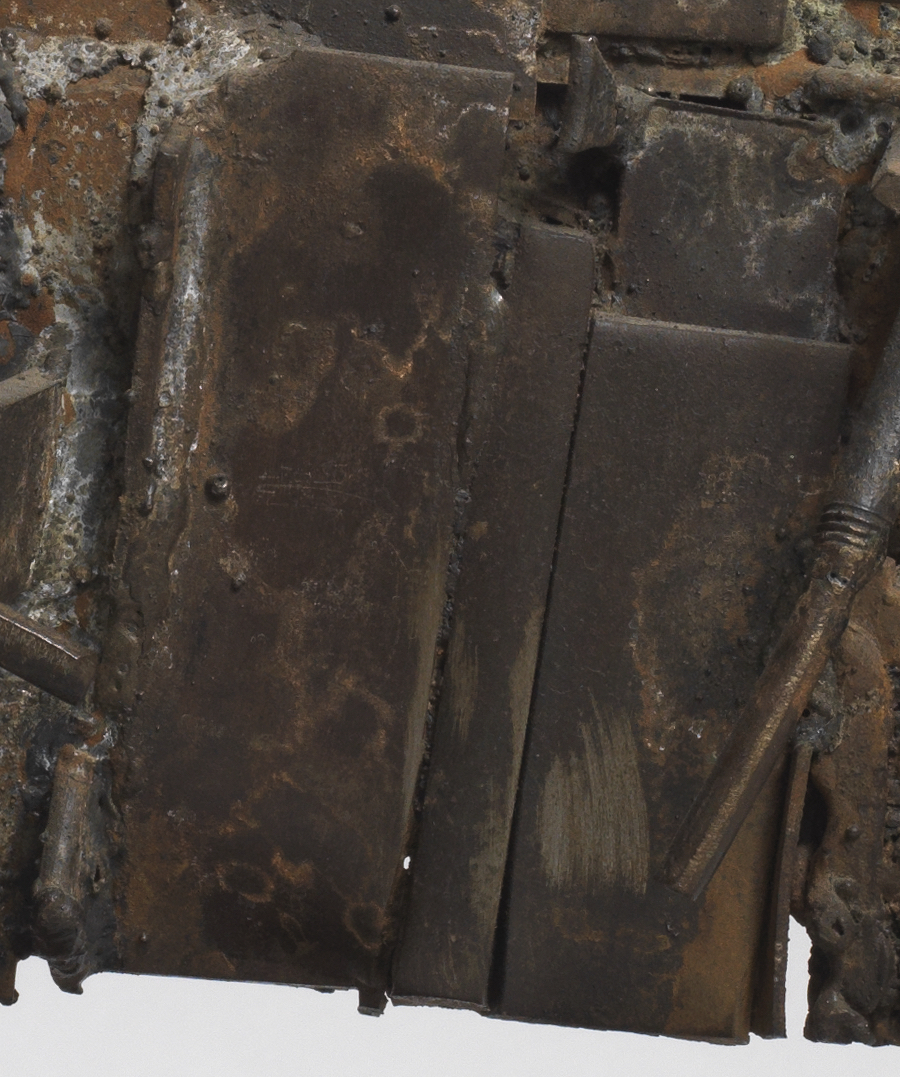
Habitation is primarily a steel sculpture, with some wrought iron. The sculpture is 32cm high, 37cm wide and 15cm deep. It has a mass of 12.5 kg.
Much of the structure of Habitation is made from thin, flat rectangles of sheet-steel. The sculpture contains at least 96 individual pieces of different shapes, sizes, and thicknesses.
These pieces of steel are off-cuts from much larger sheets. The larger sheets were most likely used in the manufacture of industrial machinery and motor vehicles. These off-cuts were what was left over after a sheet had been cut to size. They were discarded in the scrap metal yard where, had they not been picked up by César, they would have eventually been sorted into different types and recycled into new steel sheets or other steel objects.
As well as the 96 pieces of sheet steel, Habitation contains at least 20 identifiable steel objects. Some of these items are picked out on the two images below. It is unclear if Habitation has a side intended as front or back. The sculpture will be displayed in The Science Museum with the side that is below labelled ‘primary view’ facing forward. This was the side photographed in the Hanover Gallery’s 1960 César exhibition catalogue in which Habitation was first displayed.
To learn more click on any areas outlined orange in the images below.
NB: Currently this feature works best on desktop devices.
Habitation – Primary View
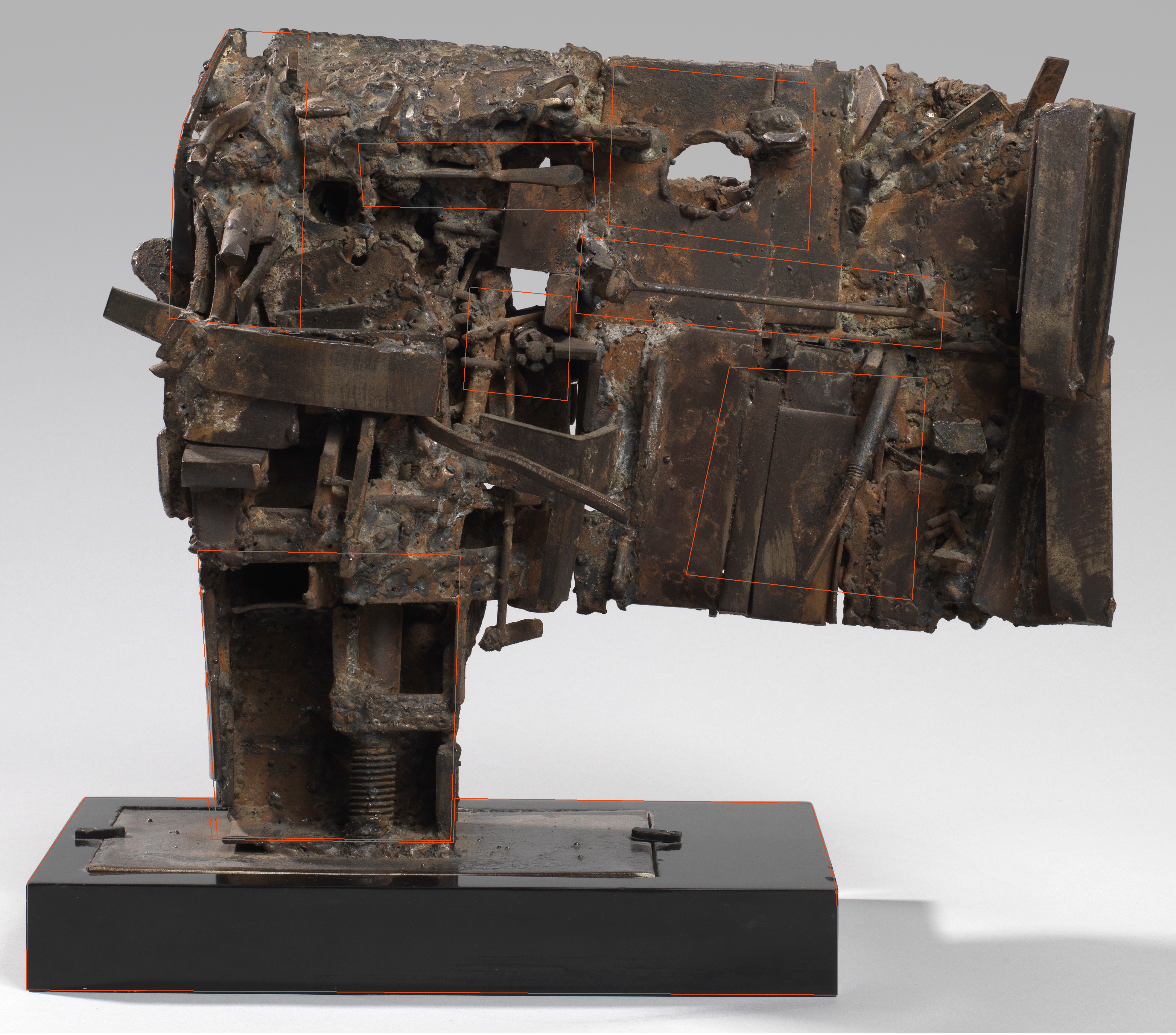
Habitation – Secondary View
This webpage has been researched and written by Jack Monaghan as part of the McQueens Illuminating Objects Series. Foremost thanks to McQueens Flowers for their support, and to Richard Eagleton and Sophie Powell in particular for their energy and enthusiasm. Special thanks to Ben Russell at The Science Museum, London for energetically opening up the wonders of iron and steel, and to Dr Shaun Crofton of Imperial College, London for so passionately (and humorously) bringing welding to life. Huge thanks too for Karin Kyburz’s and Eva Bensasson’s very patient help. Finally, I am deeply indebted to Katy Barrett at The Science Museum, and Alexandra Gerstein at The Courtauld Gallery for their meticulous, wise and enlightening counsel.

Sculpture and Decorative Arts including Illuminating Objects is proudly supported by McQueens Flowers.